Turning part is the use of lathe in the lathe on the product processing into a part of the use of the workpiece rotation and the tool of the linear motion or curve movement to change the rough shape and size, it processed into the requirements of the drawings. Turning is the use of the workpiece in the lathe relative to the tool rotation of the workpiece cutting method. The cutting energy of the turning is mainly provided by the workpiece rather than the tool. Turning is the most basic and most common method of cutting, in the production occupies a very important position. Turning is suitable for machining the rotating surface. Most of the workpieces with slewing surfaces can be machined with turning methods such as inner and outer cylindrical surfaces, inner and outer conical surfaces, end faces, grooves, threads and rotary forming surfaces. The accuracy of turning is generally IT11-IT7, and some can reach IT6, the surface roughness Ra can reach 12.5-08um. We are called turning parts and turning parts, and there are many kinds of turning parts, and it is famous for hard turning to keep the parts' thermal stability.
The first reasonable hard turning system can reduce or even eliminate the need for grinding and associated high tool costs and too long processing times. A reasonable hard turning process can be used to obtain 0.0028mm surface finish, 0.0002mm roundness and ± 0.005mm diameter tolerance, the goal of hard turning is to take at least 80% of the heat with the chip. This accuracy can also be achieved in the same machine tool as the "soft turning" of the workpiece before hardening, thus maximizing the utilization of the equipment. However, some factories have chosen to use a blade or do not know whether the machine used is sufficiently rigid to withstand twice the pressure of ordinary turning, which makes the hard turning process not fully exploit its high efficiency.
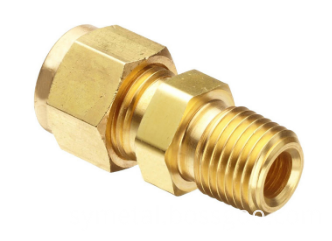
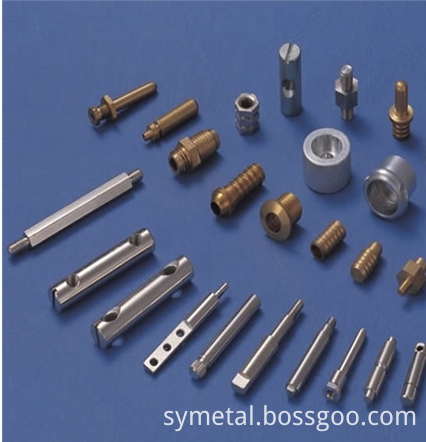