Breakdown of Industrial Process Ovens
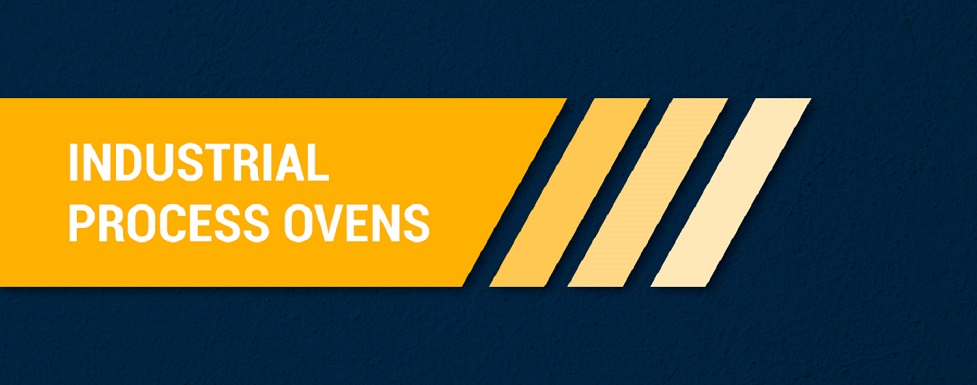
Manufacturing is a complex process involving multiple steps, all designed to produce high-quality goods efficiently. Heat plays a vital role in many of these processes, making the right thermal equipment—such as industrial process ovens—critical for success. These ovens are used across a wide range of industries, including electronics, food processing, chemical manufacturing, and more.
Selecting the appropriate oven involves careful evaluation of factors such as temperature control, airflow patterns, and compatibility with your workflow. The type of oven you choose will depend on the size of your operations, the materials you're working with, and the specific requirements of your production line. A well-chosen oven can significantly enhance productivity, reduce waste, and improve product consistency.
Contact Us
What Is an Industrial Oven?
Industrial ovens are specialized heating chambers designed to maintain precise temperature levels for a variety of applications. They are similar to kilns but offer greater flexibility in terms of temperature range, airflow control, and material handling. Depending on the model, they can be used for curing, drying, aging, and even sterilization processes.
Heating sources for industrial ovens vary and can include electric, gas, steam, or oil-based systems. The choice of heat source depends on the application, energy efficiency, and operational costs. Additionally, the design of the oven's airflow system is critical for ensuring even heat distribution and optimal performance. Common airflow configurations include horizontal, vertical, and multi-zone setups, each suited for different types of products and processes.
Are There Different Types?
Industrial ovens come in several varieties, each tailored for specific applications and production scales. Choosing the right type ensures that your oven meets your operational needs effectively. Here are the three main categories:
Laboratory Ovens
Laboratory ovens are ideal for small-scale testing, research, and sample preparation. They are commonly used in scientific and chemical applications where precision and control are paramount. These ovens typically feature stainless steel interiors, chemical-resistant coatings, and advanced temperature controllers. Their temperature ranges usually span from ambient up to around 650°F, and their sizes vary from compact units (as small as 2 cubic feet) to larger models (up to 32 cubic feet).
Industrial Batch Ovens
Batch ovens are suitable for medium to large-scale production, offering greater capacity and higher temperature ranges compared to laboratory models. They are commonly used for curing, baking, and drying processes. These ovens come in two main types: shelf (cabinet) ovens and truck (walk-in) ovens. They often include features like adjustable ductwork, aluminized steel interiors, and digital temperature controllers. Operating temperatures can reach up to 1,250°F, making them ideal for heavy-duty applications.
Conveyor Ovens
Conveyor ovens are designed for continuous production lines, where products move through the oven on a conveyor belt. They are best suited for high-volume manufacturing, especially for small to medium-sized items. These ovens typically have multiple heat zones and can operate either continuously or in an indexing mode. They also offer a maximum temperature of 1,250°F and are ideal for automated processes requiring consistent and efficient heating.
What’s the Process of Industrial Ovens?
Using an industrial oven involves several key steps to ensure optimal results. Understanding the process helps you maximize efficiency and achieve consistent outcomes. Here are the four main stages involved:
- Loading your batch: Before starting, it's important to properly prepare your load. This includes considering the heat required to raise the temperature of your materials, accounting for heat loss through exhaust, and preheating the oven to the desired level before loading.
- Heating the oven: Once the batch is loaded, the oven must be heated to the required temperature. This can be done manually using a set-point controller or automatically with a ramp and soak programmer, which allows for multiple temperature stages.
- Regulating temperature: Maintaining a stable temperature throughout the process is crucial. Soak times are often used to ensure that the product reaches and maintains the correct temperature, measured using thermocouples to monitor the difference between the product and the oven environment.
- Cooling down: After the process is complete, the oven must be cooled down. This can be done manually or via a programmed cooling cycle, allowing room temperature air to enter and circulate within the oven.
Contact Finishing Systems
At Finishing Systems, we specialize in providing reliable and high-performance industrial ovens tailored to meet the needs of various industries. With over 45 years of experience, we’ve worked with leading companies in construction equipment and vehicle manufacturing, delivering custom solutions that enhance productivity and quality.
Whether you need a laboratory oven, a batch oven, or a conveyor oven, our team of experts can help you find the perfect fit for your operation. We offer a wide range of products, professional installation, and ongoing support to ensure your success.
Improve your finishing process with Finishing Systems — contact us today to learn more about our services and how we can help you achieve better results.
Contact Us Today
China high end finned evaporator, source factory, competitive price,Direct Sales Refrigeration Copper Fin,Tube Fin Aluminum Refrigerator Evaporator Coil,Fin-And-Tube Evaporator Details Customizable
Our company has always had strict quality control standards in the market of refrigeration and heat exchange equipment, focusing on providing customised services to our customers. Not only do we have high requirements for the selection of raw materials, but we also keep up to date with the latest production processes and have high testing standards.
Our company mainly produces products for:Fin Evaporator.Fin Type Condenser.Capillary Tube. Coolant Reservoir.Plate Reinforcement Parts.Stamped Parts.Aluminum Tube.Instrument Testing Equipment.
If you have any interest, please feel free to contact us. We can provide customized service according to your drawings or samples.
Fin Evaporator,Finned Tube Radiator,Microchannel Fin Aircooler,Heat Exchanger Evaporator
Xinxiang Yukun Refrigeration Technology Co.Ltd , https://www.yukunevaporator.com